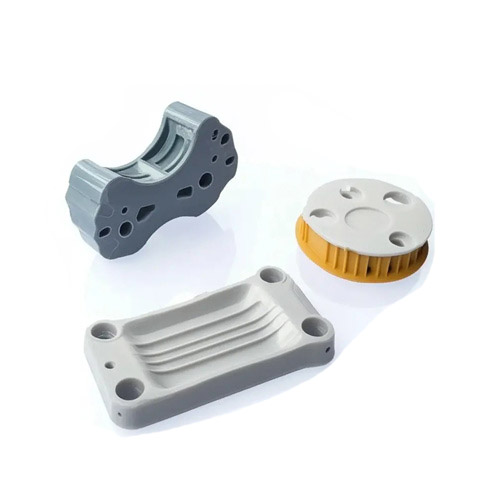
Plastic Injection Molding
Plastic injection molding is a method where plastic materials in pellet form are fed into an injection molding machine. The machine heats the pellets until they turn into a molten state. Under high pressure, the molten plastic is then injected into a pre-designed mold cavity. After a period of cooling and solidification within the mold, the mold opens and ejects the formed plastic part. This process is highly automated and efficient, enabling the production of a large number of plastic parts with consistent quality.
Materials of Plastic Injection Molding
ABS Injection Molding: ABS (Acrylonitrile Butadiene Styrene) is a thermoplastic known for its excellent impact resistance, good mechanical properties, and aesthetic appeal. It is often used in applications where both strength and appearance are crucial. In injection molding, ABS can be easily shaped into complex forms and is suitable for a variety of products.
PP Injection Molding: PP (Polypropylene) is a lightweight, flexible, and chemically stable material. It has good heat resistance and is highly durable. PP injection molding is widely used due to its cost-effectiveness and the material’s ability to withstand various environmental conditions.
PE Injection Molding: PE (Polyethylene) comes in different densities, such as LDPE (Low Density Polyethylene) and HDPE (High Density Polyethylene). LDPE is flexible and suitable for products requiring softness, while HDPE is more rigid and offers high strength, making it ideal for heavy-duty applications.
PET Injection Molding: PET (Polyethylene Terephthalate) is a transparent, strong, and shatter-resistant plastic. It is mainly used in the production of packaging materials, especially bottles and containers, due to its excellent barrier properties and ability to preserve the quality of the contents.
PS Injection Molding: PS (Polystyrene) is a clear, inexpensive plastic with good insulation properties. It is often used in applications where transparency and low cost are priorities, such as in disposable products and some decorative items.
POM Injection Molding: POM (Polyoxymethylene) is a high-strength, rigid, and low-friction material. It has excellent dimensional stability and is commonly used in mechanical and precision applications where high performance and reliability are required.
Applications of Plastic Injection Molding
Construction: In the construction industry, plastic injection molding is used to produce a variety of components. For example, window profiles made by injection molding using PVC or other suitable plastics offer good insulation and weather resistance. Plastic connectors and fasteners produced through this process are also widely used due to their corrosion resistance and ease of installation.
Toy: The toy industry extensively utilizes plastic injection molding. It allows for the production of colorful, detailed, and durable toys in large quantities. From action figures and building blocks to toy vehicles, injection molding enables the creation of complex shapes and designs that meet the safety and quality standards of the toy market.
Home Appliances: Many components in home appliances are made by plastic injection molding. The outer shells of refrigerators, washing machines, and microwave ovens, as well as control panels, knobs, and handles, are often produced through this process. Plastics used in these applications can be designed to be heat-resistant, scratch-resistant, and aesthetically pleasing.
Hardware Tools: Plastic injection molding is used to manufacture parts of hardware tools. For instance, the handles of tools like screwdrivers and pliers are often made by injection molding to provide a comfortable grip and good insulation. Some tool housings and small plastic components are also produced in this way to reduce weight and cost.
Medical Devices: In the medical field, plastic injection molding is used to produce a wide range of devices and components. Syringes, medical tubing, and some surgical instrument handles are commonly made by injection molding. The process allows for the production of sterile, biocompatible, and precise plastic parts that meet strict medical standards.
Sports Goods: Plastic injection molding plays an important role in the production of sports goods. Items such as bicycle helmets, sports equipment housings, and some sports accessories are made using this process. The materials can be chosen for their lightweight, shock-absorbing, and durable properties to enhance the performance and safety of the sports products.
Advantages of Plastic Injection Molding
High Volume Production: It is highly efficient for mass production, capable of producing a large number of parts in a short time, which helps to reduce the unit cost of each part.
Dimensional Precision: The process can achieve high levels of dimensional accuracy, ensuring that the produced parts fit together perfectly and meet the required specifications precisely.
Design Flexibility: It allows for the creation of complex shapes and intricate details that would be difficult or impossible to achieve with other manufacturing methods, providing great freedom in product design.
Good Surface Finish: The molded parts usually have a smooth and uniform surface finish, eliminating or reducing the need for additional finishing processes and improving the overall appearance of the products.
Disadvantages of Plastic Injection Molding
High Initial Costs: The investment in injection molding equipment and tooling is substantial, making it less economically viable for small-scale production or one-off projects.
Lengthy Tooling Lead Time: Designing and manufacturing the molds can be time-consuming, which may cause delays in the production process, especially for complex or customized parts.
Material Limitations: While there is a wide selection of plastics available, some specialized or high-performance materials may be more difficult to process by injection molding and may require additional technical expertise and equipment.