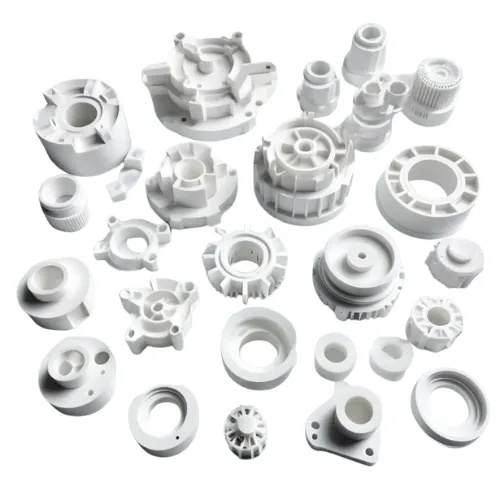
Plastic Injection Molded Parts
Plastic injection molding is a method of manufacturing plastic products of various shapes using plastic molding dies for thermoplastic or thermosetting plastics. Firstly, the plastic raw materials are added to the barrel of the injection molding machine. After heating, the materials are melted into a molten state. Then, under the push of the screw or plunger of the injection molding machine, the molten plastic is injected into the closed mold cavity. After cooling and solidification, the mold is opened, and the molded plastic part is taken out.
Advantages
High production efficiency: It can achieve automated production and produce a large number of plastic parts in a short time, which is suitable for mass production.
High dimensional accuracy: It can produce parts with high dimensional accuracy and good repeatability, meeting the requirements of various precision products.
Strong adaptability to complex shapes: It can manufacture plastic parts with very complex shapes, meeting the design requirements of different products.
Good surface quality: The molded parts have a smooth surface and high appearance quality, reducing subsequent processing procedures.
Disadvantages
High mold cost: The cost of manufacturing injection molds is relatively high, and for small-batch production, the cost is relatively high.
Large initial investment: It is necessary to purchase injection molding machines and other equipment, and the maintenance and operation costs of the equipment are also high.
Material limitations: For some materials with special performance requirements, it may be difficult to achieve ideal performance through injection molding.
Materials of Plastic Injection Molded Parts
ABS: It has good comprehensive properties, such as high impact resistance, heat resistance, low-temperature resistance, chemical resistance, and excellent electrical properties. It is easy to process and form, and has a good surface gloss, which is often used for the casings of electronic and electrical appliances, automotive parts, etc.
PP: It has the characteristics of low density, non-toxicity, odorlessness, good heat resistance, strong chemical stability, and good mechanical properties. It also has good resistance to bending fatigue and is widely used in packaging, automotive interior parts, daily necessities, and other fields.
PE: It has the properties of low-temperature resistance, good chemical stability, and excellent electrical insulation. Different types of PE, such as LDPE, HDPE, and LLDPE, have slightly different performances and are commonly used in films, pipes, injection-molded products, etc., such as various plastic containers and film packaging.
PET: It has high transparency, high strength, good barrier properties, and chemical resistance. It is often used in the packaging industry, such as beverage bottles, food packaging, etc., and can also be used for some parts in the electronics and electrical field.
PS: It has good transparency, electrical insulation, water resistance, and processing fluidity. It is easy to form and has a good surface gloss, but it is relatively brittle. It is commonly used in daily necessities, stationery, toys, optical instruments, and other fields.
POM: It has high hardness, high rigidity, high wear resistance, good self-lubrication, and fatigue resistance, with good dimensional stability. It is widely used in the machinery, electronics, automotive, and other fields and can be used to manufacture precision parts such as gears, bearings, and cams.
Applications of Plastic Injection Molded Parts
LED Lighting: In the LED lighting field, plastic injection-molded parts can be used to manufacture components such as LED lamp housings and lamp shades. For example, lamp shades injection-molded from plastic materials with high light transmittance can evenly scatter light, improve the lighting effect, and at the same time protect the LED chips.
Electronics: Many components in electronic devices are manufactured through plastic injection molding, such as mobile phone casings, tablet computer casings, keyboard keys, and packaging casings for electronic components. These plastic injection-molded parts not only provide the appearance shape for electronic devices but also protect the internal circuits and components. They can also achieve some special functions, such as electromagnetic shielding and heat dissipation.
Electrical Appliances: In the electrical appliance field, plastic injection-molded parts are widely used, such as the casings, control panels, and various components of household appliances like refrigerators, washing machines, and air conditioners. Take the refrigerator as an example, its inner liner is usually injection-molded from plastic, which has good corrosion resistance, thermal insulation, and aesthetic properties.
Packaging: Plastic injection molding is very common in the packaging field, such as various plastic bottles, plastic boxes, and plastic trays. Plastic bottles are used to package liquid products such as beverages, cosmetics, and pharmaceuticals. Plastic boxes are used to package food, daily necessities, etc., and plastic trays are used for the transportation and storage of goods, which can improve the packaging efficiency and protect the products from damage during transportation.